-
Product Line
-
Product Category
Product
ClearDocument Type
ClearApprovals & Certifications
ClearTechnical Datasheet Category
ClearWarranty Type
ClearYears
ClearCountry
ClearLanguage
ClearClear
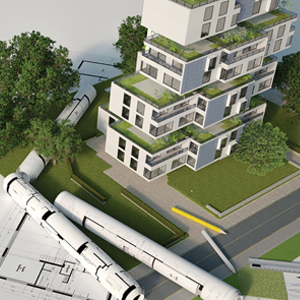
Register Your LEED Project
LATICRETE is committed to sustainability and proudly offers the LEED Project Certification Assistant. This innovative tool simplifies the LEED certification process by bundling necessary documentation and creating a downloadable LEED submittal for your projects, including documents such as HPDs, EPDs, product data sheets, and more.